Performance Analysis of Diesel Generators A Comprehensive Guide
Introduction
Diesel generators play a crucial role in providing backup power during emergencies or in off-grid locations where access to the main power grid is limited. These generators are known for their reliability, durability, and efficiency, making them the preferred choice for many industrial, commercial, and residential applications. In order to ensure optimal performance and efficiency, it is essential to conduct regular performance analysis of diesel generators. This article will provide a comprehensive guide on how to analyze and evaluate the performance of diesel generators, including key parameters to consider and best practices for maintenance and optimization.
Overview of Diesel Generators
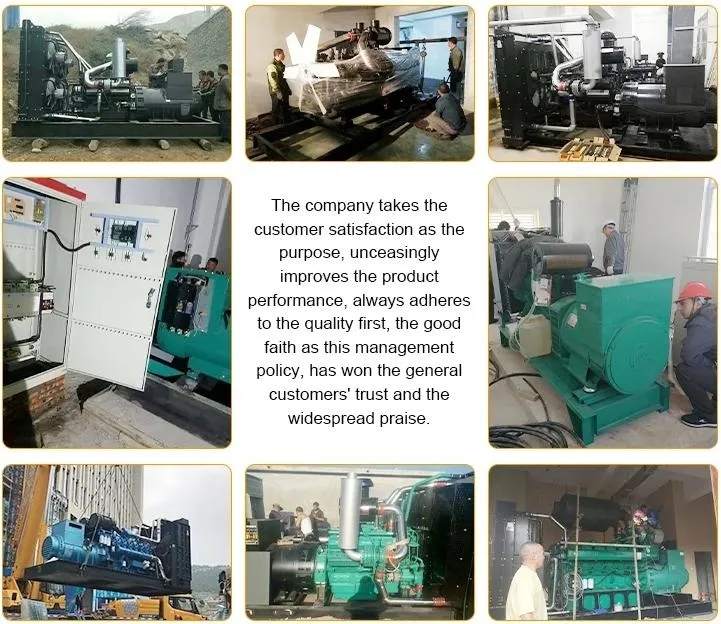
Diesel generators are a type of internal combustion engine that uses diesel fuel to generate electrical power. They consist of a diesel engine connected to an alternator, which converts mechanical energy into electrical energy. Diesel generators are widely used in various applications, including construction sites, hospitals, data centers, manufacturing facilities, and residential homes.
One of the key advantages of diesel generators is their ability to provide reliable and continuous power supply for extended periods of time. Diesel fuel is readily available and has a higher energy density compared to other fuels, making diesel generators more fuel-efficient and cost-effective in the long run. Additionally, diesel generators are known for their durability and ability to operate under heavy loads and harsh conditions.
Performance Parameters of Diesel Generators
When evaluating the performance of a diesel generator, several key parameters need to be considered. These parameters provide valuable insights into the efficiency, reliability, and overall performance of the generator. Some of the key performance parameters of diesel generators include:
1. Power Output: The power output of a diesel generator is typically measured in kilowatts (kW) or megawatts (MW). It indicates the amount of electrical power that the generator can produce under specific operating conditions. The power output of a diesel generator should match the power requirements of the load it is intended to support.
2. Fuel Consumption: Fuel consumption is a critical parameter that affects the operating cost and efficiency of a diesel generator. It is important to monitor the fuel consumption rate of the generator under different load conditions and optimize fuel efficiency to reduce operational costs.
3. Efficiency: The efficiency of a diesel generator is a measure of how effectively it converts fuel into electrical power. Higher efficiency means less fuel consumption and lower operating costs. Efficiency can be calculated as the ratio of electrical output power to the input fuel energy.
4. Voltage Regulation: Voltage regulation refers to the ability of a diesel generator to maintain a stable output voltage within acceptable limits under varying load conditions. Poor voltage regulation can lead to equipment damage and power quality issues.
5. Frequency Regulation: Frequency regulation is another important parameter that measures the ability of a diesel generator to maintain a stable output frequency (Hertz) under varying load conditions. Deviations in frequency can affect the performance of electrical equipment connected to the generator.
Performance Analysis Techniques
There are several techniques and methods available for analyzing the performance of diesel generators. These techniques help identify potential issues, optimize performance, and ensure reliable operation. Some of the common performance analysis techniques for diesel generators include:
1. Load Testing: Load testing involves applying a specific load to the generator to measure its performance under different load conditions. This test helps determine the power output, fuel consumption, voltage regulation, and frequency regulation of the generator.
2. https://www.lkpowerplant.com/product/quick-delivery-emergency-standby-power-400kw-silent-type-diesel-generator-set-for-peru/ : Fuel analysis involves testing and analyzing the quality of the diesel fuel used in the generator. Contaminated or poor-quality fuel can affect the performance and efficiency of the generator. Regular fuel analysis helps ensure proper fuel quality and combustion.
3. Oil Analysis: Oil analysis is a predictive maintenance technique that involves analyzing the condition of the engine oil to detect signs of wear, contamination, or degradation. Regular oil analysis can help prevent engine failures and optimize the performance of the generator.
4. Vibration Analysis: Vibration analysis is used to monitor the mechanical condition of the diesel generator's components, such as the engine, alternator, and cooling system. Excessive vibration can indicate misalignment, imbalance, or wear, which can lead to equipment failure.
5. Thermographic Imaging: Thermographic imaging is a non-invasive technique that uses infrared cameras to detect hot spots or anomalies in the electrical and mechanical components of the generator. This technique helps identify potential issues before they escalate into major problems.
Maintenance and Optimization Strategies
In addition to performance analysis, regular maintenance and optimization are essential to ensure the reliable operation and longevity of diesel generators. Some key maintenance and optimization strategies for diesel generators include:
1. Scheduled Maintenance: Diesel generators should undergo regular maintenance checks according to the manufacturer's recommendations. This includes oil and filter changes, fuel system inspections, coolant checks, and electrical system testing.
2. Fuel Management: Proper fuel management is essential to ensure the quality and availability of fuel for the diesel generator. It is important to monitor fuel levels, conduct fuel testing, and establish a fuel replenishment schedule to prevent fuel-related issues.
3. Cooling System Maintenance: The cooling system of a diesel generator plays a critical role in dissipating heat and maintaining optimal engine temperature. Regular inspections of the cooling system, including the radiator, hoses, and coolant levels, are necessary to prevent overheating and engine damage.
4. Battery Maintenance: Diesel generators rely on batteries to start the engine and provide auxiliary power. Regular battery inspections, cleaning, and testing are important to ensure proper functioning and avoid unexpected failures during startup.
5. Remote Monitoring and Control: Implementing remote monitoring and control systems allows operators to monitor the performance of diesel generators in real-time, receive alerts for potential issues, and remotely control the generator settings. This helps improve operational efficiency and reduce downtime.
Conclusion
Diesel generators are essential power sources for a wide range of applications, providing reliable backup power in emergencies and off-grid locations. Conducting regular performance analysis of diesel generators is crucial to ensure optimal efficiency, reliability, and longevity. By monitoring key performance parameters, using advanced analysis techniques, and implementing maintenance and optimization strategies, operators can maximize the performance of diesel generators and minimize the risk of downtime and costly repairs. Investing in proper maintenance and performance analysis can help extend the life of diesel generators and ensure a continuous and reliable power supply when it is needed most.